Safe New World
Timber Stinson-Schroff
From 1900 to 2017, the fatality rate in the American coal mining industry fell by 97%.1 What made this improvement possible? How did it affect society? Will it continue?
Despite a never-ending supply of new hazards, all forms of work have become increasingly safe. This can be partly explained by advances in technology, legislation, and/or wealth. But I feel these explanations neglect the human element.
The missing part of the story is safety protocols. I define these as intentional patterns of constraint on human behavior that reduce injury, disease, and death. Safety protocols have evolved in lockstep with changes in the industrial environment. I use the coal mining industry as a case study. Its longstanding, thorough documentation makes it a rich source. From the case study, I derive a theory of protocol evolution. I base it on a cyclical model of new protocol-based social orders emerging from old ones through mutation and selection effects.
Human ingenuity has solved problem after problem in coal mining. But these solutions have externalities (side effects). Using coal for energy kicked off a world-changing process. On the one hand, coal “would raise up not only our civilization but our very souls.”2 On the other, coal “helped create a new kind of savage existence not controlled by nature but virtually severed from it.”3 Throughout the history of coal mining, the world was getting more complex, thanks to technological progress.
Progress in coal extraction technology “reduced some risks while increasing others.”4 For example, the electrification of coal-cutting machinery eliminated dangerous mechanical parts but increased the risk of electrocution. Some externalities are predictable. But history shows we often do not know or cannot afford to care about all the consequences of our choices. How could early miners have known that burning coal would lead to global warming? How could 18th-century households have afforded to avoid air pollution if their immediate survival depended on burning coal for warmth?5
Our predictions about consequences can be wrong, ignorant, or superseded by immediate interests.6 It takes time to understand new hazards (which often arise from prior solutions) and the mix of hazards that workers must mitigate continually shifts. To cope, workers need a reliable source of short-term solutions to deal with this unstable, unpredictable mix.
Protocols are the first line of defense against hazards. We intentionally constrain our behavior to prevent exposure to hazards. For example, lockout-tagout protocols—procedures that prevent the accidental startup of machinery by physically locking it and placing warning tags—allow just one worker to power on a piece of equipment, to avoid electrocution. New norms, divisions of labor, and decision-making hierarchies emerge to enforce such constraints. This results in a new protocol-based social order.7
Technological progress, including natural science, is a key source of hazards. Protocols are the first defense. Thus new technologies quickly induce new protocol-based social orders. Nuclear power plants, airplanes, and railroads are powerful, hazardous technologies. Protocols were created as responses to their externalities. These protocols were perpetuated by new social orders. For instance, the invention of nuclear energy quickly induced a locally centralized, authoritarian social order that continues to perpetuate control over its alarming hazards.8
We have been in a centuries-long struggle against the externalities of technological progress. Inequity, social instability, and environmental degradation are awaiting resolution. In the case of safety, however, I believe the struggle has succeeded. Protocols have nearly eliminated fatal workplace accidents. We are at the end of the history of safety.9 After the case study, I’ll discuss what the future of safety will look like. But before that, what exactly is safety?
Safety as a Dynamic Non-Event
Our brains have finite bandwidth. To deal with limited memory and processing powers, we get used to things going well. The result: our brains only notice when things go wrong—when there is an event. We do not notice the non-events (i.e., the status quo, the day-to-day). But events and non-events are both consequences of human actions. No actions, no events. Action performance varies, putting the dynamic in dynamic non-event.10 Safety is a dynamic non-event. Talking about safety (and health) is difficult because it is a sustained absence of events, not an event itself.11
When you use a stapler, it’s low probability that you will prick yourself the way you might with a pin or even a paperclip. In safety terms, stapling yourself is an event. Stapling without pricking yourself is a dynamic non-event. The risk of an event is always there and you might get close to stapling your own thumb to that freshly printed pdf. Action is dynamic, and the outcome value is always slightly different. After a while, the only actions that catch our attention are those with outcome values below the “limit of unacceptable performance” (Figure 1).12
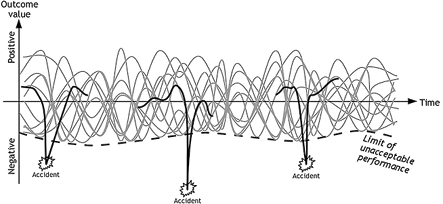
Figure 1. Hollnagel’s Outcome Value Framework showing the “limit of unacceptable performance” (dashed line)
We can easily count the times we’ve stapled ourselves (the event). It’s harder to count the times we haven’t stapled ourselves (the dynamic non-event). This is because, on the surface, all non-events are alike, where every event is eventful in its own way. It’s easier to identify discrete events. Each time you staple the paper successfully, you avoid many negative possibilities. The action’s outcome value remains above the limit of unacceptable performance and below the threshold of awareness. This is due to “moment-to-moment adjustments and compensations,13 thanks to you, the astute operator of the stapler. The same principles apply to higher-stakes situations with the well-being of others on the line.
Good safety protocols don’t just benefit individuals. They also benefit others. Reducing disease and injury improves knowledge creation and economic productivity. In other words, “The less energy expended merely in keeping a society alive, the more is available for change.”14 A few examples are listed in the table of mining safety protocols (Table 1).
Reporting an accident improves the safety of a worker by flagging a hazard for removal. The emergent benefit is aggregate information, which can facilitate investments in high-return interventions, like heart disease screening. These safety protocols all directly benefit individuals and have positive emergent effects on safety, often coordinating actors separated by space and time.
The Evolution of Safety Protocols in Coal Mining — Case Study
Pre-industrial safety protocols <1700 A.D. As early as the 13th century, Europeans started to mine coal in bell pits. Miners sunk bell pits to about 30 feet below ground, with a narrow mouth, and dug wider at the bottom. They were typically operated by a serf family and owned by a lord. It’s hypothesized that miners excavated bell pits until the structure appeared unstable, then abandoned them. A new shaft was dug nearby to access the same vein. Here we have one of the first records of a workplace safety protocol: establish a sufficient distance between bell pits so that the structural integrity of one bell pit doesn’t affect another.15, 16, 17
Drift mines were another early method of coal extraction. Miners dug a near-horizontal slope into a hillside or cliff, rather than digging a vertical shaft in a field. Dragging coal up a slope was easier and probably safer than using a ladder—but early drift mines were simple and shallow.18 As they delved deeper, coal miners disentombed a new hazard: gas. Methane was the most well-known, but there were several kinds. Each gas was identifiable by how it killed, giving them grim names:
- chokedamp: stythe, damp, or blackdamp; carbonic acid gas; an asphyxiant gas
- firedamp: methane gas/carburetted hydrogen; a highly explosive gas
- afterdamp: mix of carbon monoxide, firedamp, and nitrogen; an asphyxiant and poisonous gas
- stinkdamp: hydrogen sulfide; a poisonous gas19
The discovery of these gasses led to new safety protocols. Chokedamp is heavier than air; miners would hold a candle near the floor. If it dimmed or went out, it was time to go. Miners avoided firedamp by preemptively igniting buildups. This was initially done by a “penitent,” a convict who instead of going to jail, took on the extremely dangerous job of preemptively igniting gas build-ups.20 Miners tested nonflammable methods of illumination—they “even experimented with bringing phosphorescent fish.”21 Miners used birds like canaries to detect afterdamp and stinkdamp. Birds show symptoms faster than humans, signaling the presence of a dangerous gas. The “canary in the coal mine” was an early protocol.
Humans and animals powered pre-industrial mines. Cranks, pulleys, tools, wheels, and carts were wooden—iron was too expensive. Power sources and materials imposed limits on the scale of mining operations. Things changed dramatically with the introduction of steam engines.
The carbon flywheel 1700 to 1850 A.D. After centuries of incremental progress, the coal industry had a big bang. With the industrial revolution came steam engines, boilers, coal furnaces, new machinery, and cheaper steel. These technologies enabled a new flywheel of productivity in the coal industry. The demand for coal skyrocketed and the pace of development went exponential. Britain’s annual production was ~3 million tons of coal in 1700. About 200 years later, U.S. annual production hit ~680 million tons.22
Companies worked mines near-constantly and miners were often paid a piece wage (by the amount of coal produced, rather than time spent mining). In North America, mines were shallow, but miners worked in isolation across large areas.23 For this reason, supervision was logistically challenging and expensive. Lack of supervision plus the incentive of piece wages led miners to trade safety for productivity. (There are similar issues today with truck drivers falling asleep while trying to finish their routes faster—necessitating the need for rest protocols.)
With increased production speed, dust was a greater issue: air in mines became saturated with flammable coal dust, and silica dust, which causes tuberculosis.24 Boilers, furnaces, and explosives like Emulex were also hazardous. Heavy steel rail carts and locomotives could crush miners. Personal protective equipment was nonexistent by today’s standards.25
The combination of these changes precipitated disasters that killed tens or hundreds of miners at a time. Respiratory diseases were rampant. Workplace safety protocols were not keeping up with the pace of the industry. Workers were replaceable and unions were illegal in most of the West until the late 1800s. Miners often couldn’t afford to take precautions in their jobs.
Accumulating complexity 1850 to 1950 A.D. Coal mining safety records before around 1850 in the United States aren’t readily available. But by that time, governments were collecting data on fatalities. The grim reporting protocols tell an essential story about the philosophy of accidents. The first records didn’t even consider responsibility; clerks listed workplace deaths as inevitable, a cost of doing business.26
This period coincides with two early peaks in U.S. coal production and peak employment in the industry. Interaction between technological development and safety protocols was rapid and productive. The Bureau of Mines—established in 1910, now named the Mine Safety and Health Association (MSHA)—established mining ventilation standards. Mines had to ensure that particulate and gas levels fell under certain thresholds. Governments legalized unionization. Engineers designed equipment with safety in mind. Protocols around training, ventilation, and explosives spread.
Despite all this, terrible workplace accidents like the Monongah mining disaster happened. Called a model mine and with a sterling reputation, the mine in West Virginia exploded in 1907. Filled with chokedamp, it killed 362 people. Due to the new complexity and scale of mining operations, the root cause of the explosion was never determined.
Preventing disasters like Monongah isn’t easy, and it’s not merely an engineering problem. This era highlights the political side of safety. In the early 1900s, the U.S. government sought to ban cigarette smoking in coal mines. Today it’s obvious that was a reasonable idea. Yet, there were multiple labor strikes protesting the ban. One compelling theory: resistance to the ban was a byproduct of the traditional view of coal miners’ role and responsibilities, in that miners were viewed as craftsmen and independent contractors who were responsible for their own safety. This status, plus piece wages, suggests there were economic and social incentives to value productivity over safety. And, importantly, each worker assumed their safety was independent from every other miner’s safety. This assumption was no longer correct.
Diminishing returns 1950 to 2000 A.D. U.S. coal production peaked between 1950 and the early 2000s. At the same time, employment fell. Technology catalyzed per-worker productivity growth but also increased operational complexity. In a few centuries, the industry went from pickaxe-wielding peasant families to bulldozing megacorporations.
Protocols first appear as behavioral changes in response to newfound hazards. These protocols get built into the environment, creating rigid instead of flexible constraints on behavior. When protocols are engineered into the built environment, it frees up mental bandwidth, but a new, meta-protocol is necessary: maintenance. Specialists will emerge to sustain the rigid protocol. As a result, protocol benefits (and costs) are sustained in a scalable fashion.
Accident and fatality rates in the mining industry plunged as ventilation, detection, and respiration equipment became more effective. Protocols promoted equipment use and kept dust and gasses at benign levels. From the 1970s onwards, mining companies used atmospheric monitoring systems and automatic alerts to prevent build-ups of methane, carbon monoxide, and dust.
The protocol for deploying these systems was to space units closer than 2,000 feet apart and as high in the tunnels or chambers as possible. Following these air quality protocols would prevent explosions, cave-ins, and common mining-related diseases like black lung.27
But with so many moving parts, operations became unpredictable in and of themselves. The environment was no longer the sole source of uncertainty. Technology was now inherently safe, but accidents still occurred. This spurred changes in safety management and new approaches were trialed.
First, root cause analysis led safety experts to assume incidents were being caused by human error. If the technology is safe, then it must be the humans who mess up. But after a couple of decades of trying, researchers discovered that eliminating human error is impossible. The focus turned to sociology instead of psychology. Protocols to improve “safety culture” came about.28 Take Five (taking a few minutes to consider the risks and safety measures required for a task), Safety Walk (management walking through a workplace to identify and address hazards), Poka-Yoke (quality assurance technique aimed at making human error physically impossible), etc. emerged to fight diminishing returns on traditional approaches to safety. Still, accidents occurred.
Finally, systems theory29 came along—holding that “unexpected interactions” between “tightly coupled”30 components within a system cause accidents, and that such accidents are unpredictable. Ultimately, experts found that accidents are “normal.”31 No matter how hard we try to stop them, some will happen. These two statements are both true: all accidents are preventable and we cannot prevent all accidents.
By 2000, improvements in coal mining safety had plateaued. The rate of safety protocol evolution slowed as the safety of work approached its limits. In fact, like an autoimmune disease, safety itself was generating new hazards.
Opportunity costs 2000 A.D. to present. Increased life expectancy, food security, and sedentary jobs have presented workers with a new set of hazards like heart disease. A problem with all safety institutions is that their existence depends on chasing diminishing returns. Pivoting to new problems is difficult—requiring new knowledge and skills—but valuable. A 2006 study of MSHA concluded:
Almost 700,000 life years could be gained for typical miners if a quarter of MSHA’s enforcement budget were reallocated to other programs (more heart disease screening or defibrillators at worksites).32
That said, safety is still an issue in mining. Declining demand for coal and falling profitability in the Western world will (if it hasn’t already) create safety issues as companies’ margins shrivel. And global capitalism still has pinch points. Industries in less-developed economies are not as safe.33 The difference is that we know what to do. We have the tools. Safety is just a matter of following protocol.
But when the top work-related causes of death are health issues, overfocusing on safety is deadly. Reallocating safety budgets would save lives. Industries, insurance companies, and governmental authorities should invest in studying, creating, and spreading workplace health protocols.
Health vs. Safety
I believe we are at the end of the history of safety, and the beginning of health. In 2016, accidents caused only 25% of workplace fatalities globally.34 Disease caused the rest. Today, the top three causes of death globally are the same as the top three work-related causes of death.35 Chronic obstructive pulmonary disease (COPD), stroke, and ischemic heart disease accounted for ~63% of work-related causes of death in 2016.36
Health, like safety, is a dynamic non-event. What makes them categorically different?
They can be distinguished by differences in time and episodicity. A coal miner not using a hard hat is unsafe. A coal miner inhaling silica dust is unhealthy. A rock wall wouldn’t gradually fall onto one’s head over 10 years. It happens all at once. Inhaling dust doesn’t kill instantly, but the damage is cumulative.
In both cases, the long-run outcome is the same. Enough exposure will kill. Safety is about avoiding episodic risks of injury or death. Health is, first, about avoiding cumulative, irreparable damage. Having a pet rattlesnake is unsafe. Working a stressful job that drives you to smoke is unhealthy. Health is also about avoiding cumulative risk factors (e.g., smoking, muscle loss, obesity) that raise your chances of a fatal event.37 In that sense, safety and health overlap. Healthier = safer. The overlap is bilateral. Injuries harm workers’ abilities to live healthily. So too safer = healthier.38
The same memory mechanics (acquired unawareness of non-events) that make safety difficult are even stronger in health. Health deteriorates slowly, so it’s hard to notice a change. Limits of acceptable performance sink as we adjust our expectations to lower average levels of well-being.
Put differently, health protocols don’t have fast feedback loops, so adoption is challenging. From my experience, we operate more proactively when the risk is obvious, probable, and has the possibility of immediate harm. Safety issues trigger acute stress responses that encourage action. Anything beyond obvious risk requires empathy for a “future version of oneself” that is difficult to nurture. This can change via instrumentation, such as calorie, nutrient, movement trackers, and continuous glucose, heart rate, and sleep monitors. Anecdotal observations suggest that, when used responsibly, these can create an artificial sense of being unsafe which catalyzes healthy behavioral adaptations.
The subtle nature of health had consequences with issues like black lung and asbestos. There are several sources of friction to problem-solving in such cases. First, medical knowledge takes time to develop. Second, the scientific community can be captured and pressured to act against the best interest of workers. Corporations funding scientific research might have an interest in suppressing certain findings, as happened with miners’ silicosis.39 Third, causality is difficult to prove given the long timespan between exposure and disease (for example, asbestosis has a latency period of 15 to 30 years40), and a mechanism of harm is often below the level of human perception. I can easily see myself staple my thumb after passing on my morning coffee, but it’s impossible for me to observe arterial plaque form with my bare eyes. Fourth, health-related externalities of behavior aren’t immediate enough to provoke the formation of protocols, let alone social orders. Health consequences don’t automatically induce the creation of preventive protocols as in the case of safety—we tend to create remedies instead. These characteristics pose a challenge.
Complacent acceptance of an antiquated view of worker well-being is costing many people their lives. There is an absence of workplace health protocols that prevent the new top causes of workplace death. In 200 years, the bar has gone from don’t die to don’t get hurt to don’t burn out to love your job. Looking at today’s landscape, the world of work is a long way from solving the problems of chronic disease, burnout, and emotional health. To fill the gap, workers, policymakers, and companies need a better understanding of what protocols are and how to manipulate them.
A Grand Theory of Protocol Evolution
Protocols are born as a first response to new hazards, which arise from technological progress, environmental change, changes to the social order, and changes to the definition of safety. Because protocols limit human behavior in some way, they influence social hierarchies, soft power gradients, norms, and values. The social order directs technological progress. Technological progress changes the environment. And so on.
I have created this model (see Figure 2) based on principles of natural selection and memetic theory. Protocols evolve as a result of two opposed forces: mutation, caused by errors in protocol replication, and selection pressure, caused by many factors. A complete theory of protocol evolution must provide mechanisms for four processes: birth, mutation, selection, and death.
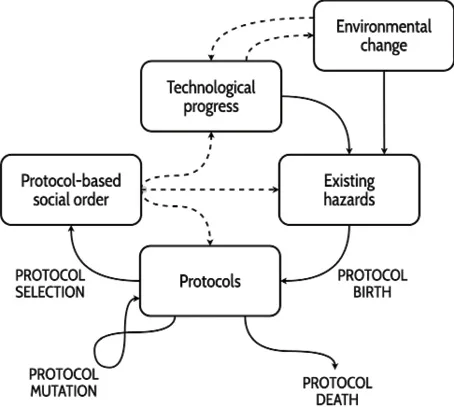
Figure 2. Tech-Protocol Cycle
Protocol birth
New protocols emerge when we encounter newly created hazards. There are three sources of hazard creation.
The first source of hazard creation in the model is environmental change, including extreme weather, changes in weather patterns, and exposure to new environments. These can change the set of hazards present in a workplace. For example, heavy rains create structural instabilities in the landscape; landslides and floods become hazards. Increasingly frequent heat waves threaten workers with heat stroke. Moving a warehouse into a floodplain would create new risks to working in that warehouse.
The second source of hazard creation is technological progress, including knowledge. Having evolved in a constantly changing natural environment, we are familiar with the kinds of hazards created by that source. Technological progress and knowledge, on the other hand, generate wide, potent, and novel sets of hazards.41 Steam engines led to mechanical machines that could deafen workers, locomotives that could crush workers, and water pumps, that enabled deep coal mines, exposing workers to novel hazards like poisonous gasses. Knowledge of how to create atom bombs created several hazards, including nuclear war.42
The third source of hazard creation is change in the social order. Safety protocols develop in response to shifts in hierarchy, power distribution, or social network size/density. For example, say a class of elites begins displacing risk onto a working class. Collectivist protocols like unionization, labor strikes, or collaborating with the press might be developed to target the source of hazards. For example, in present-day Balochistan, Pakistan, coal mine owners exploit children and immigrants for labor (owners include government officials—even the minister of mines).43 The private-public cartel protects itself with profits earned from not purchasing safety equipment. With few other options, Balochistanian miners work with international journalists to shed light on the hazards created by their nation’s abusive social order.
To sum up, new safety protocols emerge in response to new hazards created by three sources:
- environmental change
- technological progress (including knowledge), and
- social order change.
Protocol mutation
Following protocol involves several actions: perceive another person following protocol or receive instructions on how to follow the protocol; store the protocol in memory; and replicate the protocol. Errors can occur during any one of these actions. The primary way that protocols mutate is via such unintentional errors. A protocol is a type of meme: like genes, protocols reproduce using humans as hosts.
The other two ways that protocols mutate is through tinkering and design. To tinker is to intentionally mutate a protocol in some way. For example, one could add a step to a workplace inspection checklist. The pace of mutation by tinkering is likely slower than by memetic error. But it is faster and less dramatic than protocol design, which is creating or changing a protocol so that it is unique from existing protocols.
The strength of mutations from design easily places protocols into the realm of infeasibility, where actors will reject them. A corporate health and safety team designed an incident reporting protocol which workers ignored because the reports were tedious. The designed protocol landed outside of acceptable efficiency-thoroughness selection pressures and suffered an embarrassing and ignoble death. The three sources of protocol mutation, characterized by their pace and strength, are design, tinkering, and memetic error. They fall on a spectrum of pace and strength of mutation (Figure 3).

Figure 3. Protocol Mutation Pace-Strength Continuum
Differences among these sources are critical for the application of protocol studies. Tinkering appears to be the sweet spot. An aspiring protocol hacker should aim to act like a coach, rather than an engineer.
Protocol selection
If protocols merely mutated, there would be no progress. However, we saw protocols improve in the coal mining industry alongside technological development. Preventative protocols like maximum thresholds for dust and gas replaced early detection protocols like using candles. This didn’t happen overnight. Environmental factors had to change for improved safety protocols to emerge. Table 2 briefly summarizes a few of the strongest protocol selection pressures.
Protocol death (expiration)
The “birth” and “death” of protocols are intimately related. The same forces that drive protocol creation drive protocol destruction. New technologies can quickly make a protocol obsolete. Many protocols will experience slower deaths, however. A protocol could die without a favorable set of characteristics relative to its environment. Like muscles, without use, a protocol atrophies; for a protocol to die, it needs only to not be used.
Moving forward
Protocols are an overlooked building block of continually improving industries and societies. If we want to build a better world, we would be well served by an understanding of what individual actions are needed to generate public goods like safety. To use protocols to create virtuous cycles or accelerate protocol evolution, we first need to understand what protocols are. In the context of this model, one possible definition is that they are intentional constraint patterns on human behavior that address invisible concerns, like safety, health, and risk management.
This essay also suggests that evolutionary models may be a valuable analytical frame for all kinds of protocols, not just safety protocols. Using protocols as the unit of selection, and then analyzing their sources of mutation and environmental pressures improved my understanding of safety protocols.
This essay opens up several paths for future research:
- Examining the difference between health and safety. Improving workers’ long-term health outcomes is going to require fundamentally new strategies.
- Locating or developing a method to identify organizational hypersafety where returns on safety investments are negative. Overspending on safety has real costs, but I have not yet seen a method to identify thresholds.
- Exploring standards for psychological safety. We know what safety of the body is, but we don’t yet know what safety of the mind is—or if safety is even the right term. We need standards of measurement in order to make progress here.
- Assessing the strengths and weaknesses of insurance as a tool to promote worker health. I think it’s possible that mandatory insurance could help prevent things like heart disease.
- Determining if there really is a perceived decline in safety. Do people feel like life is getting more dangerous? If so, why?
Of the above, I personally am interested in exploring methods to identify hypersafety and the role of mandatory insurance in chronic disease prevention. Δ
ARTIFACT This essay is accompanied by the Self Ensured Card Collection, a twelve-suit deck that teams can use to enhance the health ergonomics of their workplaces. The deck includes protocols for movement, office design, nutrition, stress management, and company norms. Play Self Ensured with your team, a coworker, or solitaire-style!
summerofprotocols.com/research/module-three/safe-new-world
ACKNOWLEDGMENTS I’d like to thank the Summer of Protocols cohort and coordinators, Ann and Julie Stinson, Laurie Trottier, Brennan McLachlan, and Ian Vanagas for their editing prowess and/or advice.
Timber Stinson-Schroff has worked on policy, technology, and workplace safety projects in the public sector for the past four years. He’s a recovering business student with a lingering interest in organizational design and management theory. In his spare time, Timber likes to lift weights and get nerdsniped by economics and epistemology topics. He is a vanguard Gen Z and grew up as a bit of a bush kid in Yukon Territory, Canada. twitter.com/tmbr_ss
Bibliography
Abrams, Herbert. “A Short History of Occupational Health.” Journal of Public Health Policy 22, no. 4 (2001): 437–449.
Aldrich, Mark. Safety First: Technology, Labor, and Business in the Building of American Work Safety, 1870-1939. Baltimore: Johns Hopkins University Press, 1997.
Arch Resources, Our Approach to Safety. 2023.
www.archrsc.com/sustainability/safety
Attia, Peter. “Peter on the Four Horsemen of Chronic Disease.” Peter Attia, MD (blog). April 20, 2022. peterattiamd.com/peter-on-the-four-horsemen-of-chronic-disease/
Baloch, Shah Meer, and Hannah Ellis-Petersen. “‘Coal Workers are Orphans’: The Children and Slaves Mining Pakistan’s Coal.” The Guardian, February 19, 2020. www.theguardian.com/global-development/2020/feb/19/coal-workers-are-orphans-the-children-and-slaves-mining-pakistans-coal
Bainbridge, Lisanne. “Ironies of Automation.” Automatica 19, no. 6 (1983): 775–779.
Bradley, Robert. “The Rise of the Industry Continued: The 14th Century, 1301-1350.” A comprehensive history of mining in the Derbyshire, Nottinghamshire and Leicestershire Coalfields (website). 2014. www.healeyhero.co.uk/rescue/individual/Bob_Bradley/Bk-1/1300.html
Colinet, Jay F. “The Impact of Black Lung and a Methodology for Controlling Respirable Dust.” Mining, Metallurgy & Exploration, 37 (2020): 1847-1856. doi.org/10.1007/s42461-020-00278-7
Department of the Interior, “The Age and Depth of Mines.” Science 60, no. 1541 (1924): viii. www.science.org/doi/pdf/10.1126/science.60.1541.viii.s
Durham Mining Museum, Early Coal Mining. 2017. http://www.dmm.org.uk/pitwork/html/history1.htm
Freese, Barbara. Coal: A Human History. Cambridge: Basic Books, 2003.
Fukuyama, Francis. The End of History and the Last Man. United Kingdom: HarperCollins, 1992.
Hollnagel, Erik. “A Day When (Almost) Nothing Happened.” Safety Science, 134, 2021.
Hollnagel, Erik. Introduction to Safety II. 2019. safetysynthesis.com/onewebmedia/Introduction%20to%20S-II%20Part%202%20%28OCT2020%29.pdf
Hollnagel, Erik. Safety-I and Safety-II: The Past and Future of Safety Management. Farnham, UK: Ashgate Publishing, Ltd., 2014.
Kniesner, Thomas J., and John D. Leeth. “Data Mining Mining Data: MSHA Enforcement Efforts, Underground Coal Mine Safety, and New Health Policy Implications.” Journal of Risk and Uncertainty 29, no. 2 (2004): 83–111. www.jstor.org/stable/41761169
Merton, Robert. “The Unanticipated Consequences of Purposive Social Action.” American Sociological Review 1, no. 6 (1936): 894–904.
Mine Safety and Health Administration. Mine Disasters. 2000. digitallibrary.msha.gov
Mining Safety and Health Association. Coal Fatalities for 1900 Through 2017. 2018. www.msha.gov/coal-fatalities-1900-through-2017
Netschert, Bruce, and Sam Schurr. Energy in the American Economy, 1850–1975: An Economic Study of Its History and Prospects. Baltimore: Johns Hopkins Press, 1960.
National Museum of American History, Mining Lights and Hats. 2023. americanhistory.si.edu/collections/object-groups/mining-lights-and-hats
Perrow, Charles. Normal Accidents: Living with High-Risk Technologies. Princeton, N.J.: Princeton University Press, 1999.
Pennsylvania Historical & Museum Commission, Registers of Mine Accidents (PA) for the Anthracite Districts, 1899–1972. 1986. digitalarchives.powerlibrary.org/psa/islandora/object/psa%3Armaad
Peabody, 2021 Environmental, Social, and Governance Report. St. Louis, MO: Peabody, 2021.
www.peabodyenergy.com/Peabody/media/MediaLibrary/Sustainability/Peabody_ESG_2021-Report_FINAL.pdf
Schneider, Nathan. “Protocol Society.” Journal of Brief Ideas. May, 3, 2023. doi.org/10.5281/zenodo.8019263
Sunniside Local History Society. “Streetgate Bell Pit.” 2007. www.sunnisidelocalhistorysociety.co.uk/bellpit.html
Sagan, Leonard A., and Afifi, Abdelmonem A. Health and Economic Development II: Longevity. Austria: International Institute for Applied Systems Analysis, 1978.
South Carolina Department of Health and Environmental Control. “Asbestos Effects on Health.” Asbestos Information for Homeowners (blog). n.d. scdhec.gov/environment/your-home/asbestos/asbestos-effects-health
Taleb, Nassim Nicholas. “The Most Intolerant Wins: The Dominance of the Stubborn Minority.” Chap. 2 in Skin in the Game: Hidden Asymmetries in Daily Life. United States: Random House Publishing Group, 2018.
Weick, Karl. “Educational Organizations as Loosely Coupled Systems.” Administrative Science Quarterly 21, no. 1 (1976): 1–19.
Weick, Karl. “Organizational Culture as a Source of High Reliability.” California Management Review 29, no. 2 (1987): 112–127.
Winner, Langdon. The Whale and the Reactor: A Search for Limits in an Age of High Technology. Chicago: University of Chicago Press, 1988.
World Health Organization, WHO/ILO Joint Estimates of the Work-Related Burden of Disease and Injury, 2000-2016: Global Monitoring Report. Geneva: World Health Organization, 2021.
Wildavsky, Aaron. Searching for Safety. New Brunswick, N.J.: Transaction Publishers, 1988.
Zipf, R. Karl, Jr, W. Marchewka, K. Mohamed, J. Addis, & F. Karnack. “Tube bundle system: for monitoring of coal mine atmosphere.” Mining Engineering, 65 (2013): 57-63. www.ncbi.nlm.nih.gov/pmc/articles/PMC4545479/
1. Mining Safety and Health Association, Coal Fatalities for 1900 Through 2017 (2018). www.msha.gov/coal-fatalities-1900-through-2017
2. Barbara Freese, Coal: A Human History (Cambridge: Basic Books, 2003), p. 11.
3. Freese, Coal, p. 72.
4. Mark Aldrich, Safety First: Technology, Labor, and Business in the Building of American Work Safety, 1870-1939 (Baltimore: Johns Hopkins University Press, 1997), p. 4. Aldrich’s book thoroughly covers the history of U.S. coal mining safety until the mid 1900s and I’ve based much of this review of the history of mining on his account.
5. Freese, Coal, p. 31.
6. Robert Merton, “The Unanticipated Consequences of Purposive Social Action,” American Sociological Review 1, no. 6 (1936): 894–904.
7. Nathan Schneider, “Protocol Society,” Journal of Brief Ideas, May, 3, 2023. doi.org/10.5281/zenodo.8019263
8. Langdon Winner, The Whale and the Reactor: A Search for Limits in an Age of High Technology (Chicago: University of Chicago Press, 1988), p. 21.
9. See Francis Fukuyama, The End of History and the Last Man (United Kingdom: HarperCollins, 1992).
10. Karl E. Weick, “Organizational Culture as a Source of High Reliability,” California Management Review 29, no. 2 (1987): 112–127.
11. Similar to A.N. Whitehead’s “civilization advances by extending the number of important operations which we can perform without thinking about them.” In terms of safety, civilization advances by extending the number of important dynamic non-events which we can sustain without thinking about them, e.g., preventing smallpox.
12. Erik Hollnagel, “A Day When (Almost) Nothing Happened,” Safety Science 134 (2021).
13. Erik Hollnagel, Introduction to Safety II (2019).
14. Aaron Wildavsky, Searching for Safety (New Brunswick, N.J.: Transaction Publishers, 1988).
15. Sunniside Local History Society, Streetgate Bell Pit. www.sunnisidelocalhistorysociety.co.uk/bellpit.html
16. Durham Mining Museum, Early Coal Mining. http://www.dmm.org.uk/pitwork/html/history1.htm
17. Robert Bradley, “The Rise of the Industry Continued: The 14th Century, 1301-1350,” A comprehensive history of mining in the Derbyshire, Nottinghamshire and Leicestershire Coalfields (website), 2014. www.healeyhero.co.uk/rescue/individual/Bob_Bradley/Bk-1/1300.html
18. Department of the Interior, The Age and Depth of Mines, Science 60, no. 1541 (1924): viii. www.science.org/doi/pdf/10.1126/science.60.1541.viii.s
19. Bradley, “The Rise of the Industry Continued.”
20. Bradley, The Rise of the Industry Continued.
21. Freese, Coal.
22. Bruce Netschert and Sam Schurr, Energy in the American Economy, 1850–1975: An Economic Study of Its History and Prospects (Baltimore: Johns Hopkins Press, 1960).
23. Herbert Abrams, “A Short History of Occupational Health,” Journal of Public Health Policy 22, no. 4 (2001).
24. Abrams, “A Short History of Occupational Health.”
25. National Museum of American History, Mining Lights and Hats (2023). americanhistory.si.edu/collections/object-groups/mining-lights-and-hats
26. See for example, Pennsylvania Historical & Museum Commission, Registers of Mine Accidents (PA) for the Anthracite Districts, 1899–1972, preserved in the Pennsylvania State Archives digital collection. digitalarchives.powerlibrary.org/psa/islandora/object/psa%3Armaad
27. R. Karl Zipf, Jr., W. Marchewka, K. Mohamed, J. Addis, and F. Karnack, “Tube bundle system: for monitoring of coal mine atmosphere,” Mining Engineering, 65 (2013): 57-63. www.ncbi.nlm.nih.gov/pmc/articles/pmc4545479
28. Erik Hollnagel, Safety I and Safety II (2014), p. 62–104 passim.
29. Hollnagel, Safety I and Safety II, p. 121.
30. Karl Weick, “Educational Organizations as Loosely Coupled Systems,” Administrative Science Quarterly 21, no. 1 (1976): 1–19.
31. Charles Perrow, Normal Accidents: Living with High-Risk Technologies (Princeton, N.J.: Princeton University Press, 1999).
32. Thomas J. Kniesner and John D. Leeth, “Data Mining Mining Data: MSHA Enforcement Efforts, Underground Coal Mine Safety, and New Health Policy Implications,” Journal of Risk and Uncertainty 29, no. 2 (2004): 83–111. www.jstor.org/stable/41761169
33. Leonard A. Sagan and Abdelmonem A. Afifi, Health and Economic Development II: Longevity (Austria: International Institute for Applied Systems Analysis, 1978).
34. World Health Organization, WHO/ILO Joint Estimate of the Work-Related Burden of Disease and Injury, 2000-2016: Global Monitoring Report (Geneva: World Health Organization, 2021), p. viii.
35. World Health Organization, p. 13.
36. World Health Organization, p. 12.
37. Peter Attia, “Peter on the Four Horsemen of Chronic Disease,” Peter Attia, MD (website), April 20, 2022. peterattiamd.com/peter-on-the-four-horsemen-of-chronic-disease/
38. Safety and health are not perfect substitutes. Becoming completely safe will not make you completely healthy. Even in the absence of external stressors (minor incidents), internal feedback loops will destroy a system (you).
39. Abrams, “A Short History of Occupational Health.”
40. South Carolina Department of Health and Environmental Control, “Asbestos Effects on Health,” Asbestos Information for Homeowners (website), n.d.
41. Wildavsky, Searching for Safety, p. 53.
42. Knowledge can also allow us to discover existing, but unknown hazards. Discovering that cigarettes are carcinogenic, led governments to label them as a hazard. The hazard already existed, but because it was not known, safety protocols could not intentionally target it. Equivalently, the illusion of knowledge can lead us to create useless protocols, like superstitious miners whistling to ward off goblins.
43. Shah Meer Baloch and Hannah Ellis-Petersen, “‘Coal Workers are Orphans’: The Children and Slaves Mining Pakistan’s Coal,” The Guardian, February 19, 2020. www.theguardian.com/global-development/2020/feb/19/coal-workers-are-orphans-the-children-and-slaves-mining-pakistans-coal
Table 1. Mining Safety Protocols
Mining safety protocol |
Individual benefit |
Emergent group benefit |
Group meeting and risk review before entering mines |
Increased knowledge of risks and how to avoid them |
Reduced chance of one member compromising group safety |
Annual Mine Emergency Response Development exercise |
Faster and better response to well-known types of mining emergencies |
Reduces the total harm in the case of an emergency |
Reporting workplace accidents and near misses |
Root cause of the incident is fixed |
Enhanced ability to allocate investments |
Proactively alerting coworkers of your presence by flashing high beams at mine shaft intersections |
Many potential accidents (collision, exposure) are averted |
Operations are uninterrupted due to lost time |
Using signs to indicate the presence of a hazard |
Worker can rely less on memory |
First-timers know to avoid area |
Rotating inspection and monitoring duties |
Workers spend less time on cognitively draining tasks |
Performance goes up as a result of heightened attentiveness |
Table 2. Protocol selection pressures
Selection pressure |
Description |
Efficiency-Thoroughness Trade-Off (ETTO) |
Safety protocols that greatly reduce accidents will be more likely to propagate, as long as they do not reduce productivity too much. Safety protocols with steep productivity costs are less successful. |
Power/influence |
Actors with power or influence, such as the extremely wealthy, can coerce other actors into following a protocol that benefits them. Low-power actors cannot. Protocols that help those with power are more likely to replicate. |
Agency/freedom |
High-agency actors can easily opt-in and opt out of following protocols. Low-agency actors cannot. Protocols that impose high personal costs if they are not followed are more likely to replicate. Workers in a free market have more agency than indentured servants. |
Bandwidth (cognition, memory, physical) |
Actors’ abilities to perceive, remember, and replicate protocols are limited by cognition, memory, and physical bandwidth. Protocols engage in zero-sum competition for these resources. This selects protocols that are easy and cheap to mimic accurately. |
Network size, density, and openness/flow rate |
Protocols “live” on human networks. Network size, density, and openness (the maximum rate of information flow between actors) are all important factors in protocol selection. A network acts as a sort of memory. Large, dense, and high-flow networks provide a substrate for protocols that are more difficult to mimic. Small, sparse, low-flow networks kill complex protocols. Small companies cannot host as many protocols. The departure of a single employee can deeply harm the “memory” of the network. |
Technology |
Augments worker bandwidth by encoding protocols into technology, thereby freeing up bandwidth. Gas detection using candles was an active protocol, which was encoded into passive Atmospheric Monitoring Systems. More tech = more protocol capacity. Changes the ETTO of existing protocols. More effective insulation for residential houses led to problems with radon, which increased the value of existing radiation detection protocols. Enables the discovery and understanding of new hazards, like the role of lipoproteins as a risk factor for heart disease. |
Speed of costs and benefits (feedback loops) |
Protocols with immediate benefits are more likely to replicate. Short-term interests, like survival and status games, select protocols with immediate benefits. Health protocols face lots of competition from immediately beneficial protocols. The opposite is true for costs—the less immediate the costs of following protocol, the more likely it will be followed. |
Legibility of costs and benefits |
Protocols with legible benefits are more likely to be mimicked. Eye protection provides more legible benefits than hearing protection. The opposite is true for costs—the less legible the costs of following protocol, the more likely it will be followed. |
Generality of benefits |
Protocols that benefit a larger variety of actors are more likely to replicate. Anti-smoking protocols benefit not just smokers, but surrounding actors. |
Agnostic adjacent networks |
If a group has an absolute preference for following a protocol AND that protocol can be followed by the surrounding network, that protocol is likely to replicate. Food processing protocols, like a nut-free facility, are a good case. Not everyone can eat nuts, but everyone can not eat nuts. |
Ethics |
The ethics of an individual affect their acceptance or rejection of protocols. Early 20th-century coal miners, viewing themselves as entrepreneurs, might have had an ethic that favored risk-taking. |
Horizon of concern |
Longer horizons of concern, unlocked by longevity and or wealth, allow protocols with non-immediate benefits to compete. Workers focused on meeting near-term needs like food, water, and shelter don’t have the luxury to follow protocols that will benefit them only in 20+ years. |
Wealth |
The level of wealth in an industry will affect workers’ horizons of concern, their options for employment, and the amount of resources that can be reasonably spent on safety protocols. As the value of human life increases, so does the value of safety protocols. And vice versa. |
Displacement |
Some safety protocols displace costs from one group onto another, e.g., SUVs are safe, but reduce the safety of other drivers and pedestrians. The more risk a protocol displaces, the more power its participants need. A social order’s tolerance for risk displacement affects protocol selection. |
Public attention |
Protocols that target well-publicized risks might replicate better. For example, concerns over consumer food poisoning led to improvements in factory sanitation protocols, achieving the target objective and reducing the rate of occupational disease at meatpacking plants in the process. |
© 2023 Ethereum Foundation. All contributions are the property of their respective authors and are used by Ethereum Foundation under license. All contributions are licensed by their respective authors under CC BY-NC 4.0. After 2026-12-13, all contributions will be licensed by their respective authors under CC BY 4.0. Learn more at: summerofprotocols.com/ccplus-license-2023
Summer of Protocols :: summerofprotocols.com
ISBN-13: 978-1-962872-10-2 print
ISBN-13: 978-1-962872-36-2 epub
Printed in the United States of America
Printing history: March 2024
Inquiries :: hello@summerofprotocols.com
Cover illustration by Midjourney :: prompt engineering by Josh Davis
«abstract, coal mining safety protocol, exploded technical diagram»
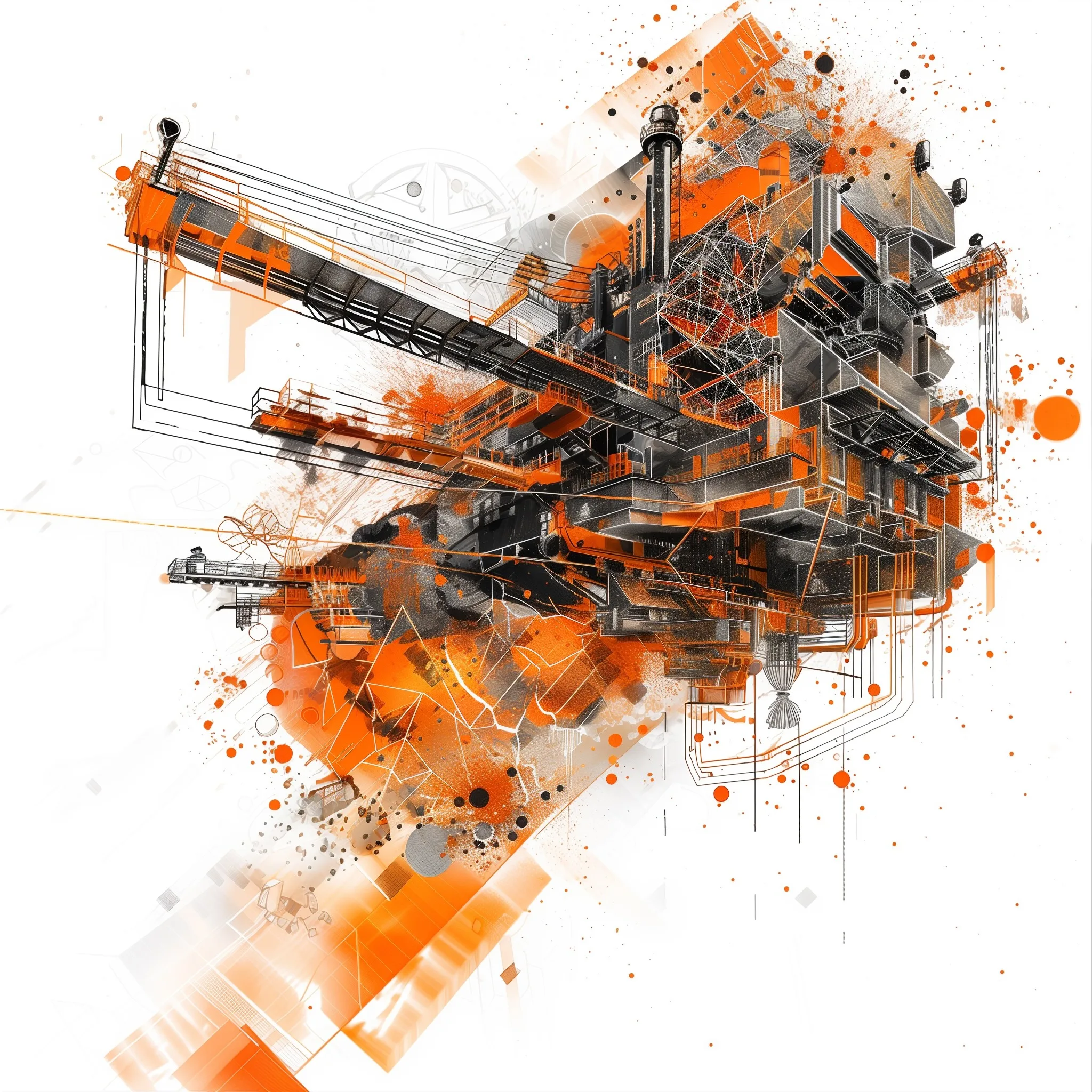